Support-Free Hollowing
IEEE Transactions on Visualization and Computer Graphics,
2018
|
|
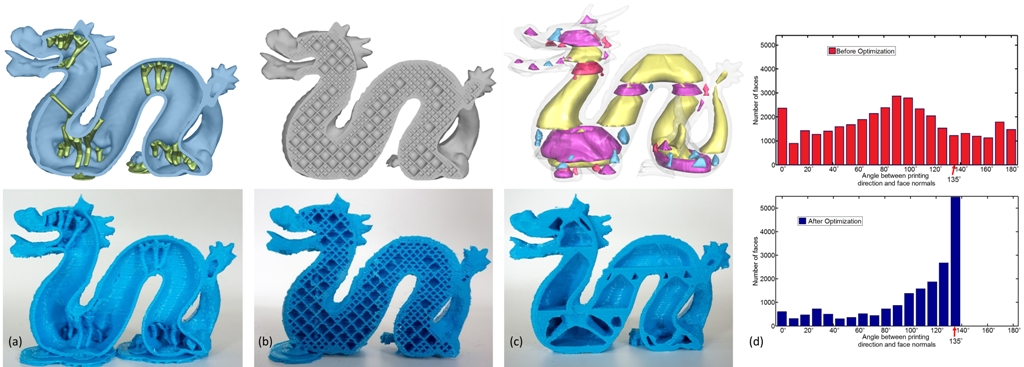
Teaser: Different from (a) conventional hollowing that needs a large number of additional supporting structures and (b) the rhombic infill structure [11]
that can only reduce 38:0% material usages, the hollowing operation developed in our framework can be repeatedly applied to a model for generating
highly sparse interior structures and optimizing different physical properties – the result shown in (c) with 69:9% less material used than the original
solid model. Our hollowing framework generates interior voids with self-supported surfaces – no supporting structure is needed for 3D printing. (d)
The histograms of the angles between surface normals of interior voids and the printing direction comparing (a) and (c).
|
Abstract |
Offsetting-based hollowing is a solid modeling operation widely used in 3D printing, which can change the model’s physical
properties and reduce the weight by generating voids inside a model. However, a hollowing operation can lead to additional supporting
structures for fabrication in interior voids, which cannot be removed. As a consequence, the result of a hollowing operation is affected
by these additional supporting structures when applying the operation to optimize physical properties of different models. This paper
proposes a support-free hollowing framework to overcome the difficulty of fabricating voids inside a solid. The challenge of computing a
support-free hollowing is decomposed into a sequence of shape optimization steps, which are repeatedly applied to interior mesh
surfaces. The optimization of physical properties in different applications can be easily integrated into our framework. Comparing to
prior approaches that can generate support-free inner structures, our hollowing operation can reduce more volume of material and thus
provide a larger solution space for physical optimization. Experimental tests are taken on a number of 3D models to demonstrate the
effectiveness of this framework.
|
Keywords |
Shape optimization, support-free, hollowing, topology variation, 3D printing |
Motivation |
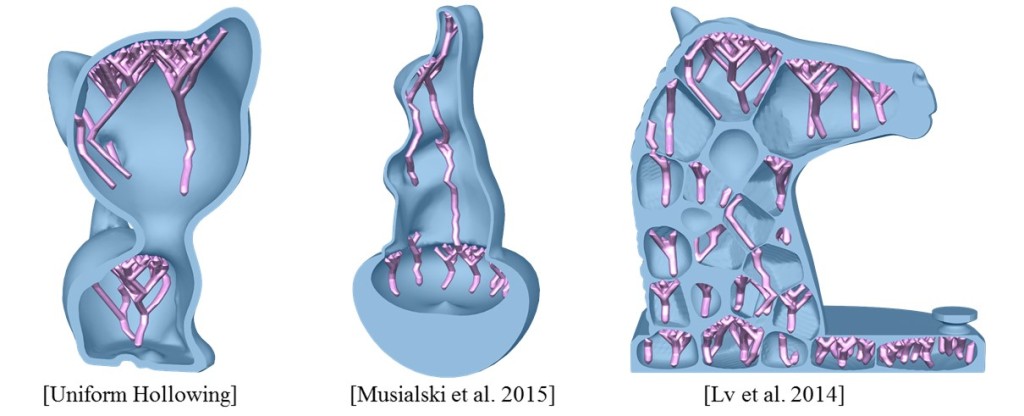
The conventional way of hollowing
for reducing the material usage in 3D printing is based
on the offsetting operator in solid modeling. Most of recent
work focuses on how to efficiently compute the offsetting,
e.g., using distance-fieldray-rep and parallel
computing. When fabricating the hollowed voids generated
by uniform offsetting, supporting structures cannot be
avoided. Non-uniform offsetting with varying thickness has
been recently employed to design the physical properties
of printed models in different aspects. For example, the
static and dynamic stability is improved in. Non-uniform
offsetting is also used to control the elastic deformation. However, the problem of avoiding interior
supporting structures has not been tackled in any of these
prior approaches.
|
Method |
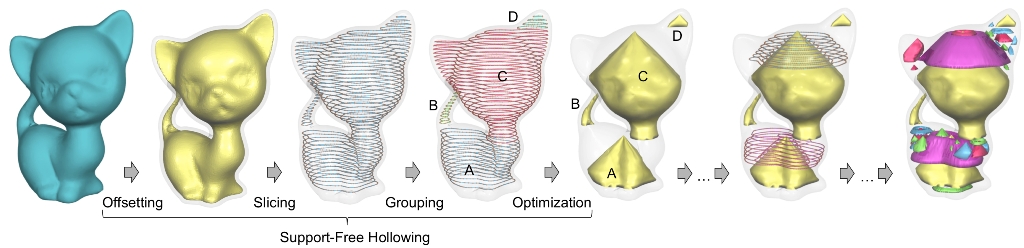
Pipeline for computing the support-free hollowing on a solid model. From left to right, an input model, the surface after uniform offsetting, the
sliced contours for hollowing, the grouping result by topology analysis for voids generation (slices in different groups, A-D, are displayed in different
colors), and the optimized interior voids that are support-free. The support-free hollowing can be repeatedly applied until no more void can be
formed – see the rightmost figure as the result with 39 voids. |
Results |

The volume of a Dragon model can be significantly reduced after repeatedly applying the hollowing operation developed in our framework –
inner voids generated in different rounds of hollowing are displayed in different colors. From left to right, the operations result in a volume reduction
of 42.9%, 57.6%, 61.1%, 64.9% and 66.6% respectively.
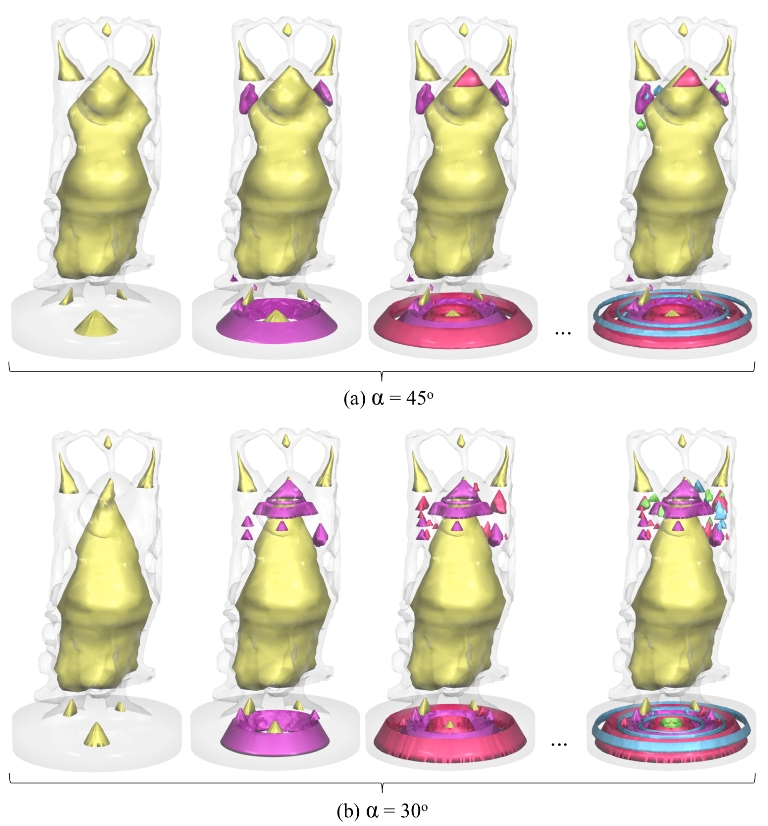
Progressive results of repeatedly applied support-free hollowing
with different maximal self-supporting angles, α. The resultant hollowing
voids have a total volume of 4.931 × 103 mm3
for α = 45◦ (a), and
4.514 × 103 mm3
for α = 30◦ (b).
|
Comparison |
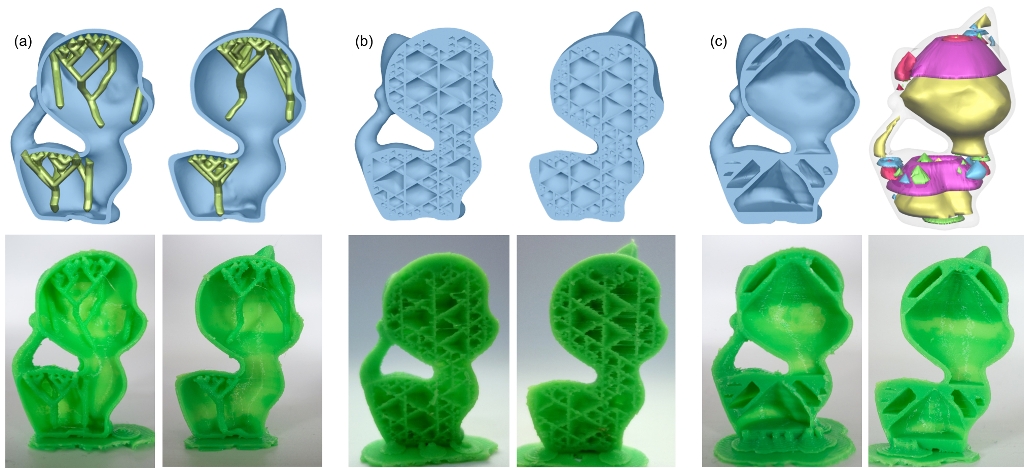
Comparison of the results generated by different methods on the Kitten model – both the computational results and the 3D printed models
are shown here: (a) the result of uniform hollowing needs interior supporting structures for fabrication, (b) the result with rhombic infill structures [11]
(with 45.5% volume reduced), and (c) the result of support-free hollowing presented in this paper (with 75.3% volume reduced). |
Paper |
high-res PDF (~27M)
low-res PDF (~1M)
|
Video
|
Demo (*.avi) (43M) |
Ack |
This work is partially supported by the Natural Science
Foundation of China (61725204, 61702079, 61432003,
61628211, 61661130156, 61370143), China Postdoctoral Science
Foundation (2016M601308), and Fundamental Research
Fund (DUT16RC(3)061). C.C.L. Wang would also
thank the support of Hong Kong RGC GRF Grant (14207414)
and the Open Research Fund of Key Laboratory of High
Performance Complex Manufacturing at Central South University,
China.
|
BibTex |
@article {wang2018support,
title = {Support-Free Hollowing},
author = {Weiming Wang, Yong-Jin Liu, Jun Wu, Shengjing Tian, Charlie C.L. Wang, Ligang Liu, Xiuping Liu}
journal = {IEEE Transactions on Visualization and Computer Graphics},
volume={},
number={},
year = {2018}
}
|
|
|
Back to Homepage
|
Copyright and disclaimer:
The SOFTWARE provided at this page is provided "as is", without any
guarantee made as to its suitability or fitness for any particular
use. It may contain bugs, so use of this tool is at your own risk.
We take no responsibility for any damage that may unintentionally be
caused through its use.
|
Copyright © 2018 GCL , USTC |
|